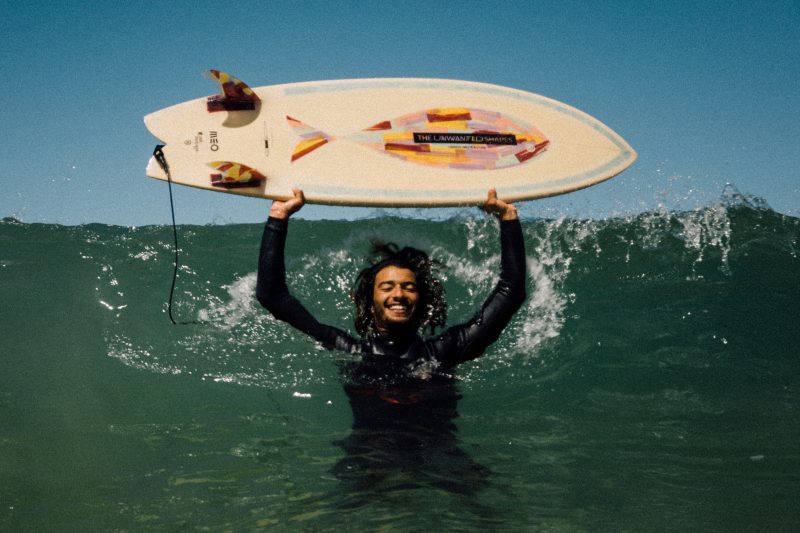
8 NGOs for Ocean Protection every Surfer needs to know
Check out the following list to discover NGOs for Ocean Protection
view story
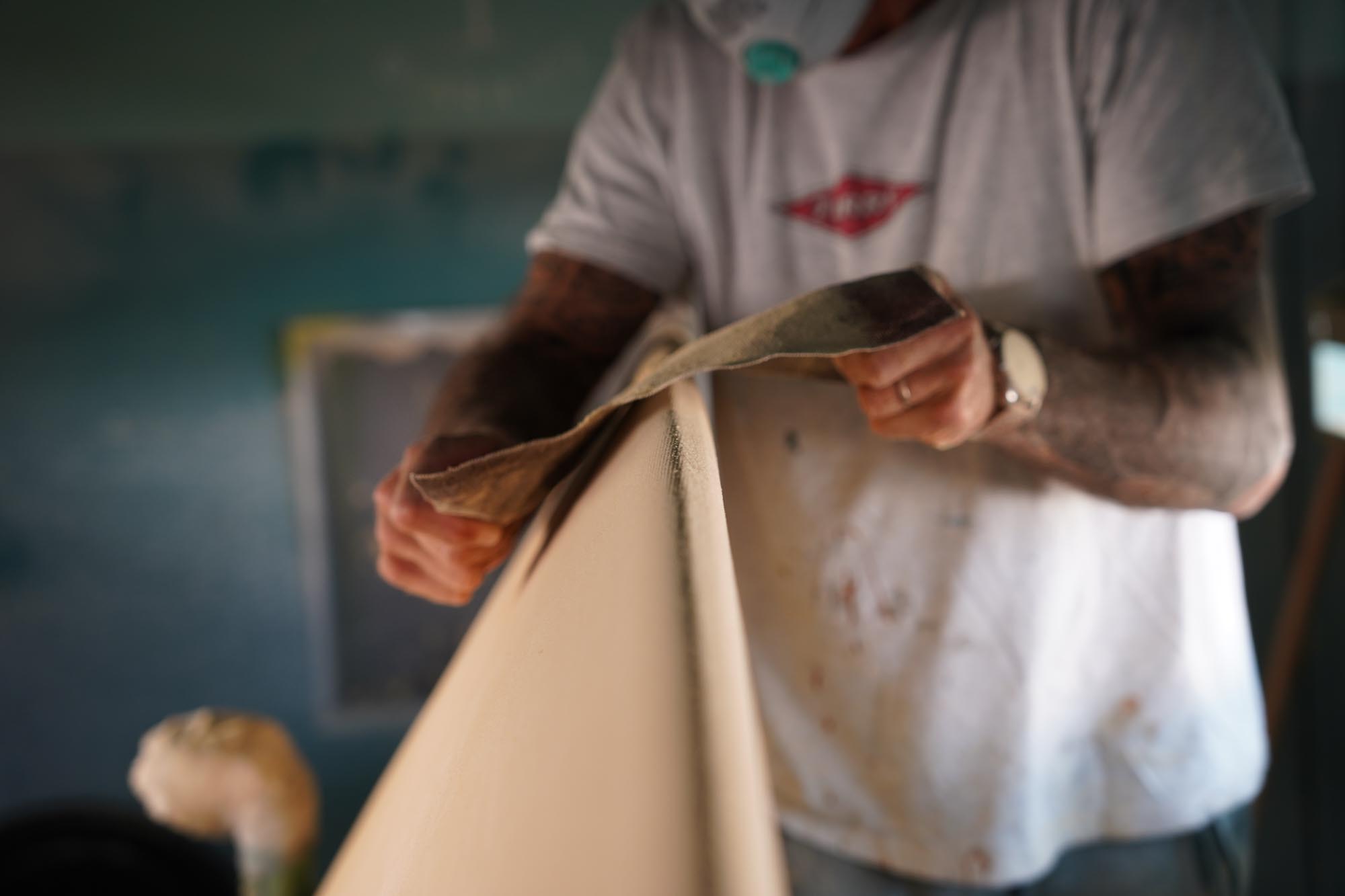
How to Shape your own Surfboard – Part 2 the blank shaping process
Explore the blank shaping process in Part 2 of our surfboard DIY guide. Learn essential techniques to shape the perfect board!
view story
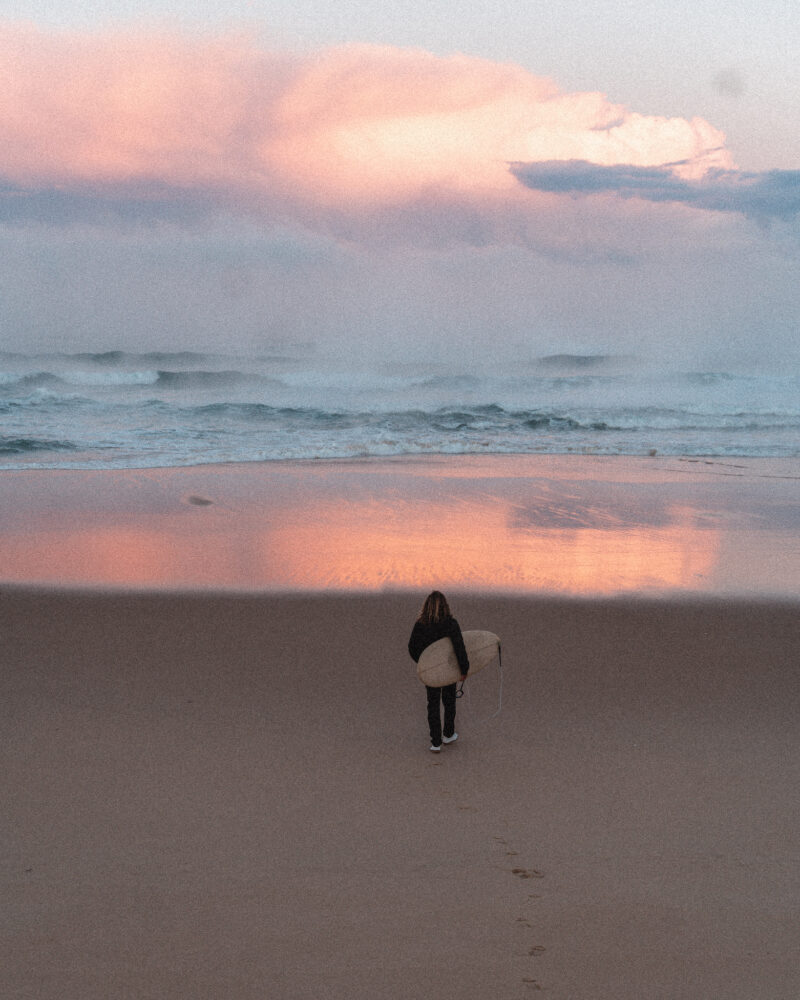
The Surfer-Environmental Paradox: Balancing Passion and Responsibility
Dive into the Surfer Environmental Paradox: discover how surfers can balance their passion for waves with sustainable practices and responsibility.
view story

The Future of Surfboard Blanks: Polyola™ Recycling PU Foam
The Polyola™ recycled PU formula: 2/3 recycled material, high performance, and sustainability for modern surfboard blanks.
view story
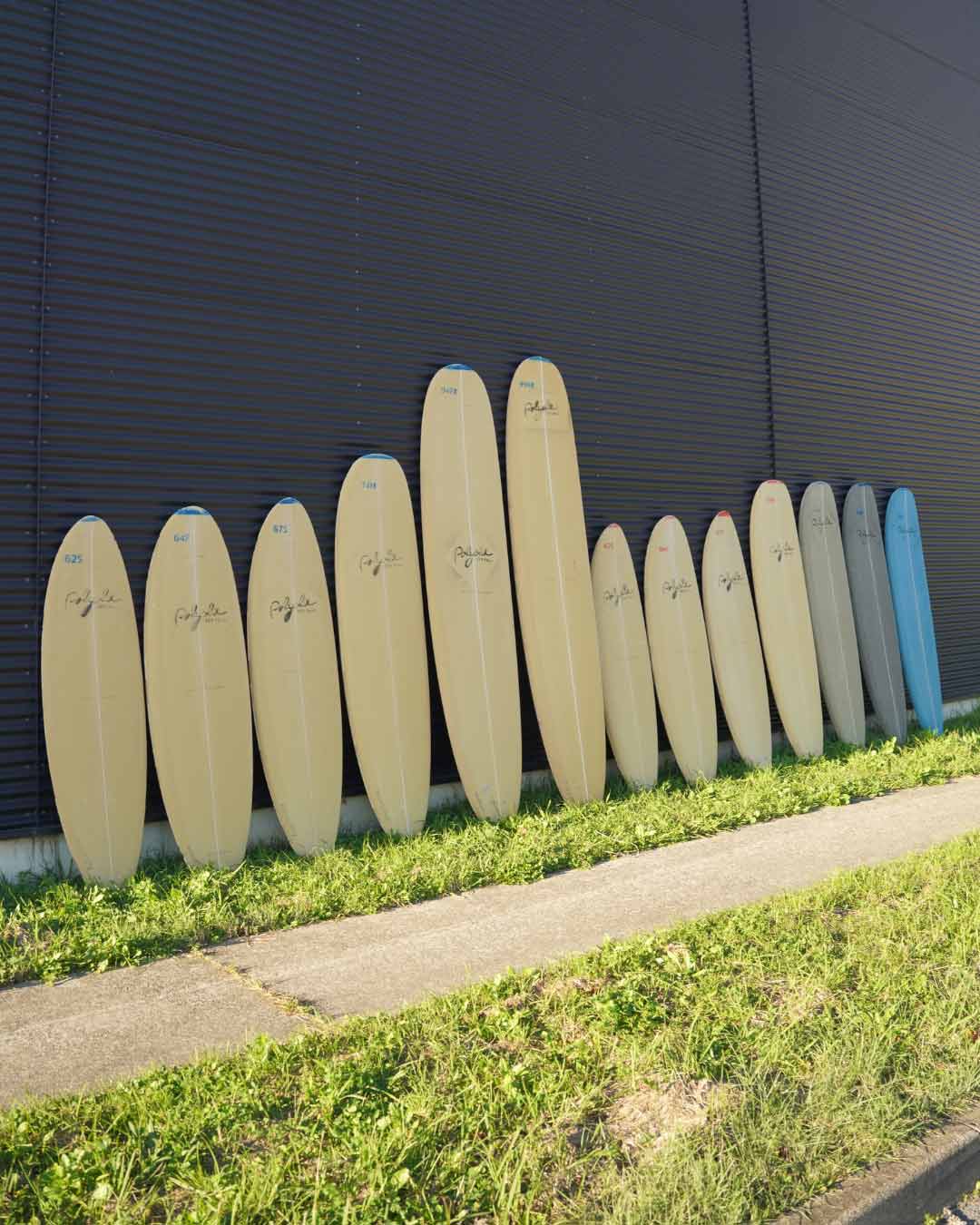
Revolutionize Surfboard Manufacturing with Sustainable Surfboard Blanks
In the ever-evolving world of surfing, sustainability is becoming a top priority.
view story
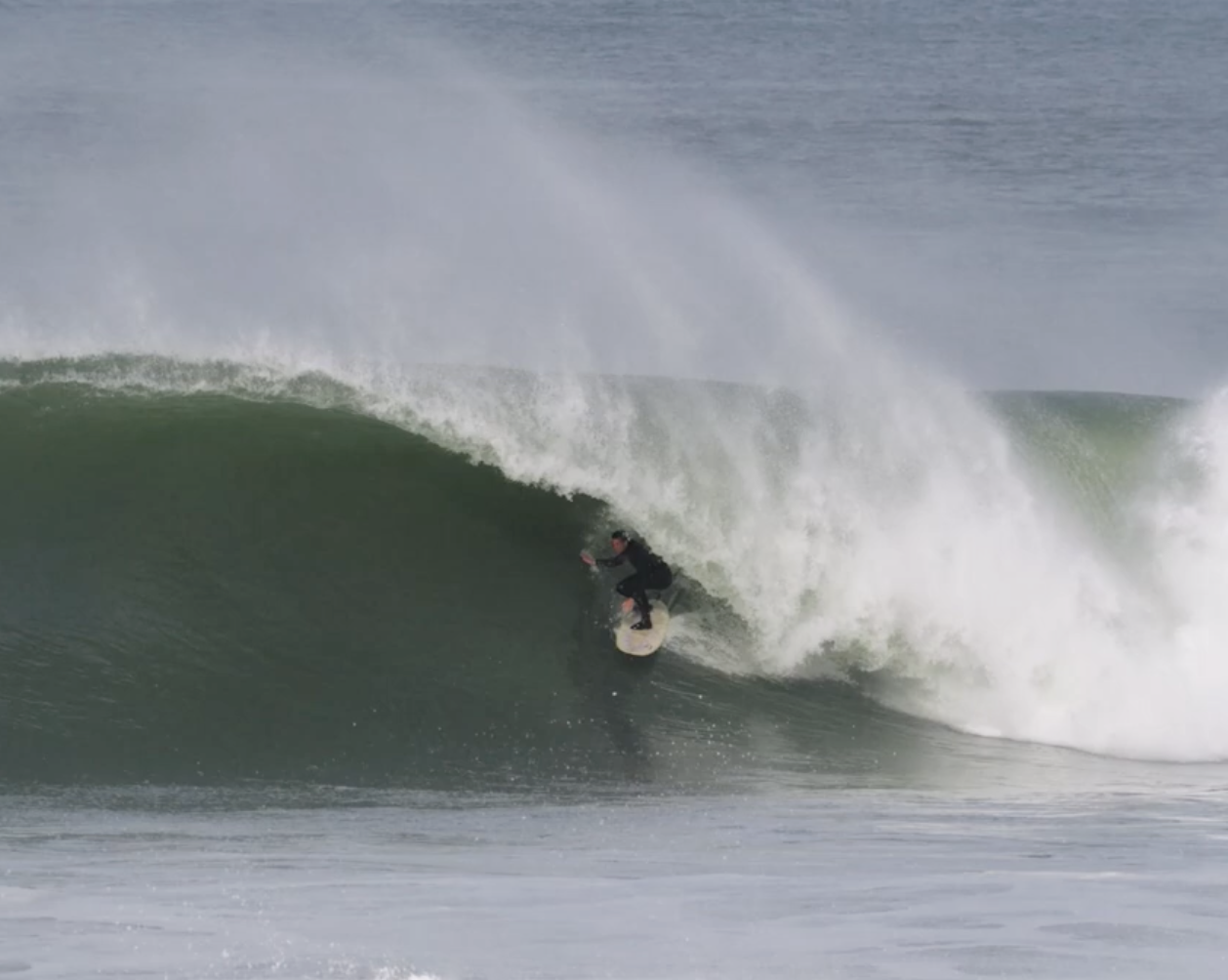
Vincent Duvignac & Boris Romann: Chasing Winter Swells in Hossegor
Vincent Duvignac and Boris Romann charge Hossegor’s winter swells and rip on boards made with Polyola™ Foam.
view story
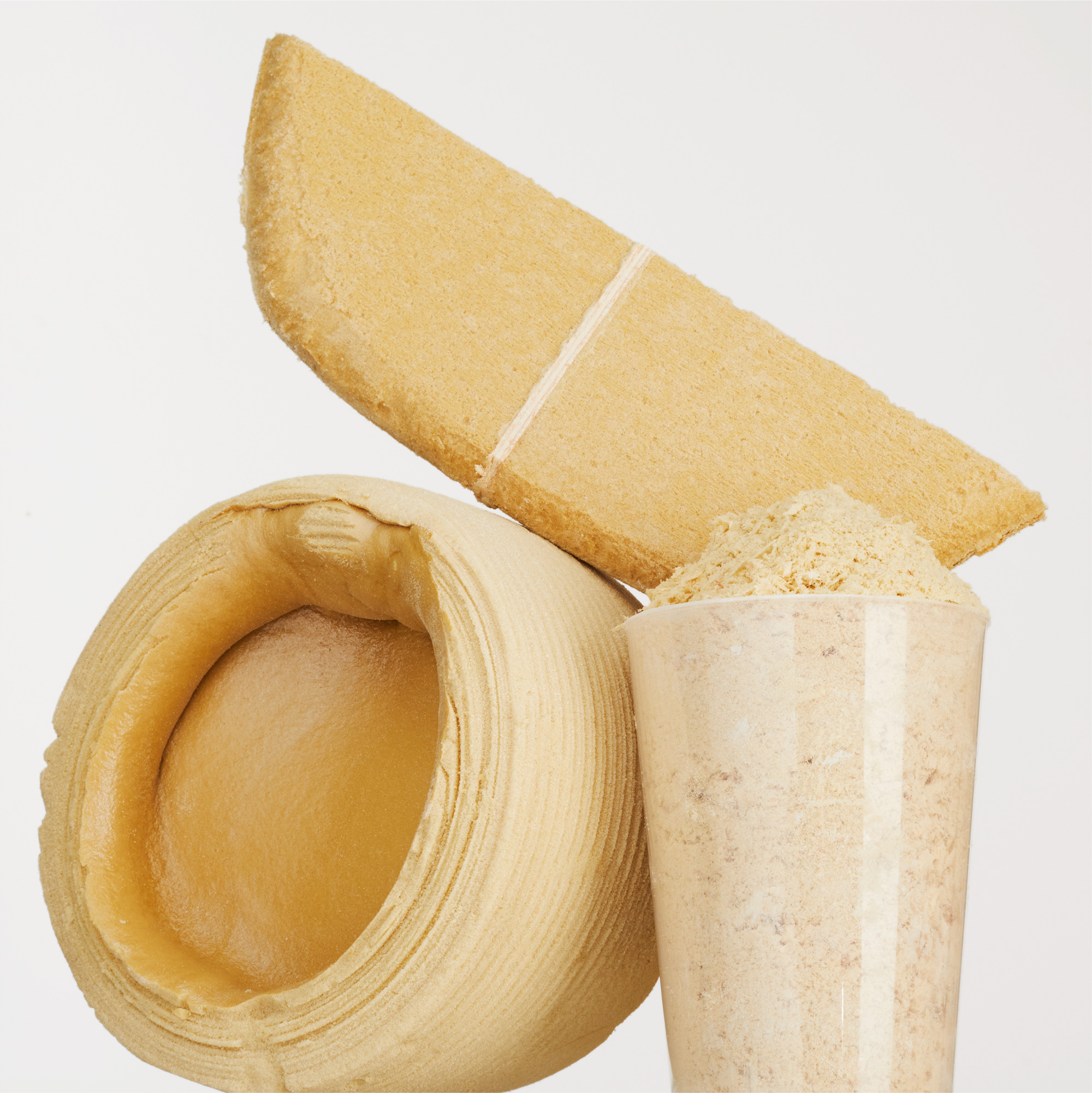
EPS vs. PU Foam Surfboard Blanks: Key Differences and How They're Made
Compare EPS and PU surfboard blanks. Learn their differences in production, performance, and sustainability, and why PU foam dominates the industry.